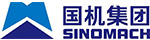
文章出處:知識(shí)中心 網(wǎng)責(zé)任編輯: 洛陽(yáng)軸承 閱讀量: 發(fā)表時(shí)間:2021-07-28 09:05:55
提高軸承疲勞壽命從而提高資源利用率的一種方式是改善表面和次表面的特性。由文獻(xiàn)可知承受滾壓應(yīng)力的部件中殘余應(yīng)力對(duì)部件疲勞壽命產(chǎn)生的影響。最大載荷所引起的剪切應(yīng)力深度中的殘余應(yīng)力可持續(xù)提高軸承疲勞壽命。Voskamp在增加載荷的條件下進(jìn)行了跑合階段的軸承試驗(yàn),并在更具普遍性的載荷下持續(xù)進(jìn)行了試驗(yàn)。由于軸承在跑合階段產(chǎn)生了殘余應(yīng)力,因此對(duì)軸承疲勞壽命產(chǎn)生了積極的影響。結(jié)果表明,裝有經(jīng)上述短期增加載荷跑合階段而產(chǎn)生殘余應(yīng)力的內(nèi)圈的深溝球軸承的疲勞壽命比未經(jīng)跑合階段的軸承套圈提高了3倍。市場(chǎng)上的軸承大多通過(guò)磨削和超精工藝加工而成,這種生產(chǎn)方法產(chǎn)量高且加工表面質(zhì)量好,并且會(huì)產(chǎn)生最深20 μm的殘余應(yīng)力。與此相對(duì),采用硬車(chē)與深滾壓相結(jié)合的生產(chǎn)方法可在載荷引起的最大應(yīng)力深度處產(chǎn)生殘余應(yīng)力,同時(shí)獲得與磨削和超精后相當(dāng)?shù)谋砻娲植诙取?/span>
提高軸承疲勞壽命的第一步是開(kāi)展標(biāo)準(zhǔn)軸承次表面區(qū)域的變化研究。接下來(lái),開(kāi)發(fā)和測(cè)試硬車(chē)與深滾壓相結(jié)合的制造工藝來(lái)確定如何具體調(diào)整表面和次表面的特性。建立一種根據(jù)軸承預(yù)殘余應(yīng)力來(lái)計(jì)算軸承疲勞壽命的模型。最后,在四軸承試驗(yàn)臺(tái)上對(duì)采用新工藝加工生產(chǎn)的軸承進(jìn)行驗(yàn)證。
1、試驗(yàn)技術(shù)
使用Hembrug Microturn 100車(chē)床對(duì)NU206圓柱滾子軸承內(nèi)圈進(jìn)行硬車(chē)。該軸承材料為100Cr6鋼,經(jīng)淬火和回火后硬度為62 HRC。采用型號(hào)為DNMA150616的硬質(zhì)合金刀作為硬車(chē)刀具,通過(guò)刷涂和磨削來(lái)調(diào)整切削刃的微觀幾何形狀。這些工具由制造商提供,具有傳統(tǒng)的Al2O3+Ti(C,N)涂層。深滾壓工藝則采用靜壓滾壓工具進(jìn)行加工。
軸承在四軸承試驗(yàn)臺(tái)上進(jìn)行運(yùn)行試驗(yàn)。一方面,所謂的篩選試驗(yàn)用于記錄邊界區(qū)域特性隨試驗(yàn)時(shí)間的變化,并確定合適的表面和邊界區(qū)域特性。另一方面,進(jìn)行疲勞試驗(yàn)的統(tǒng)計(jì)。純徑向載荷下在試驗(yàn)臺(tái),上同時(shí)運(yùn)行4套試驗(yàn)軸承,且每套軸承承受相同的載荷。該試驗(yàn)臺(tái)配有潤(rùn)滑油溫控功能,可實(shí)現(xiàn)對(duì)試驗(yàn)軸承潤(rùn)滑油溫度精確控制。試驗(yàn)過(guò)程中采用黏度η40為68 mm2/s(η100為8.9 mm2/s)的全合成潤(rùn)滑油。設(shè)定轉(zhuǎn)速n為4050 r/min,油溫為60 ℃。試驗(yàn)時(shí)比油膜厚度λ不小于3來(lái)保證軸承為全油膜潤(rùn)滑。通過(guò)振動(dòng)信號(hào)監(jiān)測(cè)軸承的剝落損傷,只要監(jiān)測(cè)到損傷就立刻停止試驗(yàn)。選擇C/P為4的徑向載荷,此時(shí)軸承上產(chǎn)生的Hertz應(yīng)力pmax為2500 MPa。軸承疲勞壽命試驗(yàn)采用突然死亡法進(jìn)行。
2、硬車(chē)-滾壓工藝生產(chǎn)圓柱滾子軸承
如Denkena等人所示,由于車(chē)削和深滾壓在工藝控制上具有相似性,因此可很好地結(jié)合。滾壓球在表面的精確定位更有利于滾道表面形貌的精確加工,因此該工藝適用于制造滾動(dòng)軸承。圖1a所示的概念已被開(kāi)發(fā)用于內(nèi)圈的加工。加工刀具如圖1b所示。為確保滾壓球在進(jìn)給方向的旋轉(zhuǎn)溝道內(nèi)的定位,球徑(dk為3.175 mm)與刀片的轉(zhuǎn)角半徑(r為1.6 mm) 應(yīng)相匹配。球的定位采用楔形導(dǎo)軌,保證定位精度為±2 μm。
圖1 硬車(chē)-滾壓復(fù)合工藝工具
硬車(chē)工藝無(wú)法在保證表面粗糙度的同時(shí)獲得較好的內(nèi)應(yīng)力。加工過(guò)程中,表面粗糙度由進(jìn)給速度和切削刃半徑?jīng)Q定,切削刃半徑過(guò)大會(huì)降低其表面粗糙度,同時(shí)會(huì)在z達(dá)300 μm的深度處產(chǎn)生大的殘余應(yīng)力。
通過(guò)深滾壓工藝可有效降低表面粗糙度,同時(shí)獲得大的殘余壓應(yīng)力。進(jìn)給速度和覆蓋率u對(duì)硬車(chē)和車(chē)削-滾壓過(guò)程中表面粗糙度的影響如圖2所示。表面加工質(zhì)量?jī)H受覆蓋率u的影響。引入過(guò)程控制變量Nw作為偏移因子來(lái)描述球在表面上的位置。這里Nw為進(jìn)給方向位移χf與進(jìn)給量f之比。殘余應(yīng)力的影響原理與Hertz接觸應(yīng)力相似。殘余應(yīng)力的穿透深度隨著球尺寸的增大而增大。滾壓應(yīng)力影響殘余壓應(yīng)力的大小。密合度的增加可使深滾壓工具與相同表面積之間有更多接觸。對(duì)于這2種工藝過(guò)程之間的相互影響,僅需考慮表面粗糙度即可。硬車(chē)工藝對(duì)表面粗糙度有重要的影響,這是由于高材料硬度阻止粗糙峰在滾壓過(guò)程中完全變形,因此初始表面粗糙度也決定了最終表面質(zhì)量。深滾壓工藝主要影響殘余應(yīng)力狀態(tài)。為了研究滾壓過(guò)程中工件溫度對(duì)邊界特性的影響,在不同的工件溫度下進(jìn)行了試驗(yàn)研究。環(huán)境溫度從室溫升高至300 ℃。結(jié)果表明,隨著溫度升高,殘余壓應(yīng)力的增幅最小,并且當(dāng)溫度超過(guò)200 ℃時(shí),整個(gè)工件的硬度降低。然而,在硬車(chē)過(guò)程中產(chǎn)生的熱量?jī)H對(duì)工件局部產(chǎn)生影響。
圖2 進(jìn)給速度和覆蓋率u對(duì)后續(xù)硬車(chē)和車(chē)削-滾壓過(guò)程中獲得的表面粗糙度的影響
3、提高軸承疲勞壽命的次表面區(qū)域設(shè)計(jì)
為了量化殘余應(yīng)力對(duì)軸承疲勞壽命的影響,建立了軸承內(nèi)圈有限元模型,通過(guò)將外載荷和附加殘余應(yīng)力狀態(tài)疊加來(lái)分析滾道表面下的三維應(yīng)力狀態(tài)。該模型可輸出von Mises等效應(yīng)力、正交剪切應(yīng)力和靜壓應(yīng)力,以便采用基于loannides和Harris的方法進(jìn)一步進(jìn)行疲勞計(jì)算。
外部載荷施加在軸承套圈上產(chǎn)生三維Hertz應(yīng)力。該模型考慮了軸承滾道的真實(shí)輪廓,利用該模型可獲得疲勞極限應(yīng)力τu和疲勞應(yīng)力指標(biāo)τi,并將其作為loannides-Harris疲勞壽命模型的輸人。根據(jù)loannides等人的研究,存活概率S確定為
該概念考慮了應(yīng)力體積V中載荷引起的應(yīng)力的大小和深度。根據(jù)文獻(xiàn),對(duì)于線(xiàn)接觸,e為9/8,c為31/3 (Lundberg 和Palmgren的指數(shù)),h為7/3。使用Dang Van 指標(biāo)作為應(yīng)力相關(guān)的疲勞指標(biāo)τi。該模型的計(jì)算結(jié)果與試驗(yàn)結(jié)果進(jìn)行了對(duì)比,可在考慮殘余應(yīng)力的情況下計(jì)算軸承疲勞壽命。
4、圓柱滾子軸承的壽命評(píng)估
第一步將標(biāo)準(zhǔn)研磨的軸承作為參考進(jìn)行研究。在試驗(yàn)滾動(dòng)軸承的前3x107r(t為120 h)內(nèi),其表面和次表面的特性發(fā)生了顯著變化。研究表明,對(duì)于研磨的軸承,殘余粗糙峰發(fā)生塑性變形,產(chǎn)生殘余應(yīng)力。如Voskamp的研究所示,殘余應(yīng)力產(chǎn)生在最大剪切應(yīng)力的深度處,且其應(yīng)力值在軸承經(jīng)歷3x107r后保持恒定。
硬車(chē)軸承套圈的首次疲勞試驗(yàn)已表明這一工藝的潛在極限值。套圈的表面粗糙度過(guò)大會(huì)引起軸承過(guò)早失效,而表面粗糙度足夠低的軸承與研磨的軸承試驗(yàn)結(jié)果相當(dāng)。在疲勞壽命試驗(yàn)的跑合階段,粗糙峰減小,殘余應(yīng)力增大。與標(biāo)準(zhǔn)軸承相比,由于自制軸承的工作表面沒(méi)有凸度,會(huì)產(chǎn)生較低的最大Hertz應(yīng)力pmax(2 300 MPa),因此,在試驗(yàn)過(guò)程中使軸承產(chǎn)生了較低的殘余應(yīng)力。
隨后的深滾壓工藝使?jié)L道產(chǎn)生較高的殘余應(yīng)力并降低了表面粗糙度。在最初的3 x107r內(nèi),殘余應(yīng)力仍保持在較高的水平。與跑合階段相比,該加工工藝使軸承產(chǎn)生更大的殘余應(yīng)力,降低了軸承運(yùn)行期間的臨界剪切應(yīng)力,并可計(jì)算出提高的軸承疲勞壽命。這同樣適用于硬車(chē)軸承套圈。硬車(chē)試樣中的殘余應(yīng)力相較于車(chē)削后深滾壓試樣移動(dòng)到更深的深度,如圖3所示,在經(jīng)過(guò)t為50 h和120 h的試驗(yàn)時(shí)間后,硬車(chē)試樣的殘余應(yīng)力未發(fā)生顯著變化。
圖3 深滾壓軸承和車(chē)削-滾壓軸承的殘余應(yīng)力變化
軸承在進(jìn)行了耐久性試驗(yàn)后考慮到接觸應(yīng)力略有不同。研磨的軸承的額定壽命L10為274h,Weibull斜率值為0.6;硬車(chē)軸承的額定壽命L10為771 h;硬車(chē)隨后進(jìn)行深滾壓的軸承的額定壽命L10為1 924 h,相對(duì)于硬車(chē)工藝提高了2.5倍。研磨、硬車(chē)和隨后深滾壓加工的軸承的存活概率的理論計(jì)算與試驗(yàn)值的對(duì)比如圖4a所示。
圖4 不同工藝制造的圓柱滾子軸承的預(yù)期壽命
由于產(chǎn)生殘余應(yīng)力而使軸承疲勞壽命提高,殘余應(yīng)力幾乎在載荷引起的臨界應(yīng)力深度處達(dá)到最大值。根據(jù)已驗(yàn)證的模型,深滾壓和其他3種不同方式車(chē)削-滾壓軸承套圈的計(jì)算軸承額定壽命L10,mod如圖4b所示。在工藝設(shè)置時(shí)根據(jù)鋼球尺寸(dk為3.175 mm[HG3]和6.35 mm[HG6])和切削速度vc而異。根據(jù)計(jì)算結(jié)果可見(jiàn),經(jīng)過(guò)車(chē)削-滾壓工藝可使軸承具有產(chǎn)生足夠的殘余應(yīng)力狀態(tài)的可能性。
5、結(jié)論
由于滾動(dòng)軸承在提高部件資源利用率中占有重要作用,本研究以圓柱滾子軸承為研究對(duì)象。目的是通過(guò)采用新的硬加工工藝來(lái)設(shè)計(jì)和調(diào)整軸承滾道表面和次表面的特性,并針對(duì)不同硬加工工藝的應(yīng)用開(kāi)展了相應(yīng)的分析。考慮了次表面殘余應(yīng)力的影響,建立了在完全彈流潤(rùn)滑區(qū)域工作的圓柱滾子軸承的壽命模型。在此基礎(chǔ)上,介紹了一種新的車(chē)削-滾壓復(fù)合工藝,即硬車(chē)與深滾壓同步進(jìn)行的復(fù)合工藝。對(duì)采用硬車(chē)、硬車(chē)后深滾壓和車(chē)削-滾壓復(fù)合3種工藝制造的軸承內(nèi)圈進(jìn)行了評(píng)估。一方面考察了邊界區(qū)域特性的變化,另一方面考察了軸承疲勞壽命。研究表明,在軸承設(shè)計(jì)中如果考慮表面特性和次表面殘余應(yīng)力,可顯著提高軸承疲勞壽命。硬車(chē)和深滾壓復(fù)合制造工藝已被證明是一種可產(chǎn)生有益的殘余應(yīng)力狀態(tài)的生產(chǎn)工藝,可使軸承疲勞壽命提高2.5倍,生產(chǎn)效率提高1.4倍。在設(shè)計(jì)軸承時(shí)考慮到這點(diǎn)有助于提高資源利用率。
(參考文獻(xiàn)略)
(來(lái)源:軸承雜志社)
軸研所公眾號(hào) 軸承雜志社公眾號(hào)
營(yíng)銷(xiāo)熱線(xiàn)
0379-64367521
0379-64880626
13693806700
0379-64880057
0379-64881181