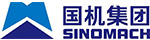
文章出處:知識(shí)中心 網(wǎng)責(zé)任編輯: 洛陽(yáng)軸承 閱讀量: 發(fā)表時(shí)間:2020-08-14 09:17:48
軸承套圈每個(gè)生產(chǎn)工序均會(huì)對(duì)其質(zhì)量產(chǎn)生影響。軸承失效分析中,套圈的材料孔洞缺陷、鍛造缺陷、熱處理質(zhì)量、磨削燒傷、環(huán)境腐蝕是導(dǎo)致軸承失效的主要原因,因此必須重視套圈的生產(chǎn)質(zhì)量,減少軸承因套圈質(zhì)量問(wèn)題而導(dǎo)致的早期失效,最終實(shí)現(xiàn)提高軸承壽命的目的。
對(duì)廢品分析軸承套圈產(chǎn)生缺陷的原因進(jìn)行統(tǒng)計(jì)發(fā)現(xiàn):材料因素是影響套圈質(zhì)量的主要因素,包括材料內(nèi)部冶金缺陷,如夾雜物、夾渣、顯微孔隙,套圈因材料外部缺陷未完全清除的殘留,如脫碳、微裂紋、表面缺陷等;其次為熱處理工藝,包括熱處理質(zhì)量不合格(組織粗大,屈氏體不符合標(biāo)準(zhǔn)要求,粗大網(wǎng)狀碳化物)和淬火應(yīng)力裂紋;另外,磨削質(zhì)量也是影響套圈質(zhì)量的主要因素之一,主要為磨削燒傷引起表層組織改變,嚴(yán)重時(shí)產(chǎn)生磨削裂紋;管理因素(人為原因)主要是指套圈生產(chǎn)過(guò)程中操作不當(dāng)引起的機(jī)械傷(劃傷、墊傷)以及環(huán)境腐蝕(酸腐蝕和氧化腐蝕),提高操作人員的責(zé)任意識(shí)及業(yè)務(wù)水平可以預(yù)防此類(lèi)缺陷的產(chǎn)生。
1、套圈常見(jiàn)質(zhì)量問(wèn)題及特征
1.1 材料質(zhì)量缺陷
材料質(zhì)量缺陷是決定軸承套圈質(zhì)量的重要因素。套圈的材料主要有棒材和鋼管。按照缺陷產(chǎn)生的部位,將材料質(zhì)量缺陷分為內(nèi)部缺陷和外部缺陷。
1.1.1 內(nèi)部缺陷
內(nèi)部缺陷主要有非金屬夾雜物、夾渣、顯微孔隙、發(fā)紋等。
非金屬夾雜物是軸承鋼冶煉過(guò)程產(chǎn)生的,無(wú)法避免,因此GB/T 18254—2016對(duì)軸承鋼非金屬夾雜物有特殊規(guī)定。非金屬夾雜物存在于套圈基體內(nèi),成為裂紋源造成套圈早期剝落;加工過(guò)程中偶爾會(huì)裸露套圈表面,造成套圈報(bào)廢。磨削滾道面的非金屬夾雜物裸露形貌如圖1所示。
圖1 外圈溝道面非金屬夾雜物殘留電鏡形貌
套圈存在肉眼可見(jiàn)的夾雜物即夾渣(主要成分為爐渣或耐火材料)時(shí),易成為裂紋源,使套圈過(guò)早損壞甚至報(bào)廢。外圈外徑面的夾渣缺陷如圖2所示。
(a) 外徑面缺陷形貌
(b)缺陷電鏡形貌
圖2 外圈外徑面夾渣缺陷
顯微孔隙又稱(chēng)顯微裂紋,金相觀(guān)察其沿晶界分布并沿軋制方向伸展。產(chǎn)生原因主要有材料中心疏松或加熱溫度過(guò)高,鋼坯心部的低熔點(diǎn)合金相熔融。若套圈中存在顯微孔隙,會(huì)極大降低晶粒間的結(jié)合力,影響套圈的力學(xué)性能;嚴(yán)重的顯微孔隙淬火時(shí)容易產(chǎn)生裂紋,若暴露至軸承零件表面則易產(chǎn)生黑點(diǎn),降低防銹性能甚至導(dǎo)致軸承產(chǎn)生疲勞剝落。外圈顯微孔隙金相圖如圖3所示。
圖3 外圈顯微孔隙金相形貌
發(fā)紋是一種存在于鋼材表皮下層的細(xì)小裂紋缺陷。產(chǎn)生原因?yàn)殇撳V中的皮下氣泡或非金屬夾雜物經(jīng)軋制變形后,存在于材料表層且沿軋制方向斷續(xù)分布,數(shù)量不等。若套圈存在發(fā)紋缺陷,易產(chǎn)生剝落掉塊。
1.1.2 外部缺陷
外部缺陷主要有材料裂紋、脫碳、凹坑等。
材料裂紋存在于棒材表層一定深度下,折疊裂紋的特征是與表面呈一定角度,裂紋中一般有氧化皮存在,裂紋兩側(cè)有脫碳現(xiàn)象。若材料裂紋在套圈中殘留必定引起質(zhì)量問(wèn)題。在套圈車(chē)削成形過(guò)程中,若材料裂紋缺陷沒(méi)有完全車(chē)除,便會(huì)在套圈上殘留,最終造成后續(xù)加工或裝配或使用過(guò)程中開(kāi)裂。內(nèi)圈外徑面鋼管裂紋殘留如圖4所示。
圖4 車(chē)削成形后內(nèi)圈外徑面鋼管裂紋殘留
材料表面脫碳,若是鋼管,主要產(chǎn)生在外圈外徑面及滾道面擋邊處和內(nèi)圈內(nèi)、外徑面,分別對(duì)應(yīng)鋼管的外徑面和內(nèi)徑面;若是棒材,材料表面脫碳指鋼材外表面。脫碳對(duì)套圈質(zhì)量的影響與裂紋相似,一方面套圈淬火時(shí)易產(chǎn)生淬火應(yīng)力裂紋;另一方面,脫碳區(qū)拉應(yīng)力較大,受外力作用易開(kāi)裂,因此,GB/T 1255—2014對(duì)軸承套圈表面脫碳層深度進(jìn)行了嚴(yán)格的控制。外圈外徑面殘留鋼管原始脫碳層如圖5所示。
圖5 外圈外徑面殘留鋼管原始脫碳層
材料表面缺陷,如較深的銹蝕坑、壓痕等,若車(chē)削成形時(shí)不能完全去除,亦會(huì)在套圈表面殘留,影響其加工質(zhì)量。
1.2 加工成形缺陷
套圈制造方式不同,其成形工藝不同。僅對(duì)工作中遇到的套圈成形缺陷問(wèn)題進(jìn)行分析。
1.2.1 鍛造工藝
鍛造是軸承套圈常見(jiàn)的加工工藝。鍛造可以細(xì)化晶粒,改善網(wǎng)狀碳化物,從而提高套圈性能。然而,若鍛造工藝不當(dāng)會(huì)產(chǎn)生鍛造缺陷,影響套圈質(zhì)量。如G95Cr18不銹軸承鋼,鍛造溫度過(guò)高易產(chǎn)生孿晶組織,這是標(biāo)準(zhǔn)JB/T 1460—2011嚴(yán)格控制的。常見(jiàn)的鍛造缺陷主要有鍛造組織過(guò)熱、過(guò)燒和鍛造折疊裂紋。
鍛造過(guò)熱組織會(huì)沿晶界析出粗大而封閉的網(wǎng)狀碳化物,嚴(yán)重的網(wǎng)狀碳化物會(huì)破壞材料的連續(xù)性,使鋼的力學(xué)性能降低,特別是沖擊韌性,而且其在退火中保持不變,只能通過(guò)正火才能消除。
過(guò)燒組織晶粒粗大,晶界局部氧化或熔融,主要原因是加熱溫度過(guò)高或保溫時(shí)間過(guò)長(zhǎng)等。GCr15軸承鋼鍛造過(guò)燒產(chǎn)生的熔融孔洞形貌如圖6所示。
圖6 鍛造過(guò)燒熔融孔洞形貌(×200)
鍛造折疊裂紋是由于切料不齊、毛刺或操作不當(dāng)?shù)仍谔兹Ρ砻嫘纬桑涮卣魇橇鸭y一般與表面呈一定角度,裂紋兩側(cè)有嚴(yán)重的脫碳層。粗磨外圈折疊裂紋形貌如圖7所示。
圖7 外圈鍛造折疊裂紋形貌
1.2.2 車(chē)削工藝
車(chē)削是軸承套圈成形的主要缺陷:一方面是不能完全清除材料表面缺陷,使套圈表面殘留,進(jìn)而影響套圈質(zhì)量;另一方面是較深切尖銳的車(chē)刀紋極易產(chǎn)生應(yīng)力集中甚至燒傷,在淬火時(shí)產(chǎn)生淬火應(yīng)力開(kāi)裂,裝配時(shí)產(chǎn)生斷裂。其主要產(chǎn)生于套圈油溝及滾道面擋邊處。外圈滾道擋邊的裂紋缺陷如圖8所示,原因是擋邊存在車(chē)削燒傷。
圖8 外圈滾道面擋邊車(chē)削缺陷(×500)
1.2.3 冷輾及串光工藝
冷輾成形也是軸承套圈常見(jiàn)的成形方式,冷輾工藝不當(dāng)造成的套圈質(zhì)量缺陷主要為冷輾裂紋。冷輾屬于冷加工,材料延展性有限,若輾擴(kuò)較大,易產(chǎn)生冷輾裂紋,另外,GCr15軸承鋼由于存在碳化物帶(碳化物偏析聚集),此處組織硬且脆,在變形過(guò)程中易拉裂。沿碳化物帶分布的冷輾裂紋缺陷形貌如圖9所示。
圖9 沿碳化物帶分布的冷輾裂紋形貌
串光是改變套圈表面粗糙度的一種方法,其工藝不當(dāng)易造成薄壁套圈產(chǎn)生磕碰傷甚至掉塊,如圖10所示。
圖10 串光工藝不當(dāng)所致的擋邊掉塊
1.3 熱處理缺陷
熱處理(主要指淬、回火工藝)是實(shí)現(xiàn)軸承套圈高強(qiáng)韌性的重要工藝,對(duì)套圈質(zhì)量的影響較大。統(tǒng)計(jì)數(shù)據(jù)表明,熱處理質(zhì)量缺陷約占套圈廢品的22.55%。常見(jiàn)的熱處理質(zhì)量缺陷主要有脫碳、淬火應(yīng)力裂紋、組織過(guò)熱及屈氏體不合格。
熱處理脫碳是指套圈淬回火過(guò)程中表層碳含量低于正常含量,可分為完全脫碳和脫貧碳。完全脫碳時(shí)套圈表層為鐵素體組織,金相下呈白色;脫貧碳時(shí)該區(qū)域馬氏體針相對(duì)基體較粗大,但均為馬氏體組織。隨著熱處理設(shè)備的改進(jìn),套圈淬回火時(shí)主要產(chǎn)生脫貧碳現(xiàn)象,會(huì)極大降低套圈表層的耐磨性和耐疲勞性能,局部產(chǎn)生拉應(yīng)力,是微裂紋源區(qū)。
嚴(yán)重的熱處理脫碳會(huì)產(chǎn)生淬火應(yīng)力裂紋,其特征是形狀不規(guī)則,深淺不一,裂紋開(kāi)口處多存在油污,金相觀(guān)察裂紋兩側(cè)無(wú)脫碳現(xiàn)象。
套圈組織過(guò)熱主要因加熱溫度過(guò)高或保溫時(shí)間過(guò)長(zhǎng)而產(chǎn)生粗大的馬氏體針。
屈氏體不符合標(biāo)準(zhǔn)要求主要是指加熱不足引起塊狀屈氏體或冷卻不良形成針狀屈氏體,宏觀(guān)表現(xiàn)為局部軟點(diǎn)即硬度不合格。外圈表面嚴(yán)重?zé)崽幚砻撎冀M織形貌如圖11所示,其在裝配時(shí)開(kāi)裂。
圖11 外圈熱處理脫碳組織形貌
1.4 磨削缺陷
磨削是軸承加工過(guò)程的關(guān)鍵工序,是實(shí)現(xiàn)套圈精度尺寸要求的重要加工工藝。根據(jù)統(tǒng)計(jì)結(jié)果,磨削質(zhì)量缺陷主要指磨削燒傷、磨削裂紋及其他磨削缺陷。磨削燒傷指表層組織燒傷(高溫回火),降低表面耐磨性;磨削裂紋導(dǎo)致套圈開(kāi)裂,整批報(bào)廢,經(jīng)濟(jì)和時(shí)間損失巨大。
軸承套圈磨削燒傷常見(jiàn)于滾道面、內(nèi)外徑面以及端面,其特征是內(nèi)外徑面及滾道面呈振紋狀或斑塊狀,端面燒傷多呈斑塊狀。磨削燒傷冷酸洗后呈灰黑色,金相觀(guān)察組織呈暗黑色。磨削燒傷冷酸洗組織形貌如圖12所示。
圖12 套圈磨削燒傷冷酸洗組織形貌
磨削裂紋多為龜裂狀,深度較淺,金相觀(guān)察裂紋兩側(cè)無(wú)脫碳現(xiàn)象。磨削裂紋常伴有嚴(yán)重的磨削燒傷,但磨削燒傷不一定產(chǎn)生磨削裂紋。套圈磨削過(guò)程中,其表層應(yīng)力狀態(tài)較復(fù)雜,磨削裂紋的產(chǎn)生是綜合應(yīng)力的結(jié)果,因此分析其產(chǎn)生原因時(shí)需綜合考慮,尤其是磨削前各工序的加工質(zhì)量,如車(chē)削質(zhì)量、熱處理變形等。外圈內(nèi)徑面熱酸洗磨削裂紋形貌如圖13所示。
1.5 裝配質(zhì)量缺陷
圖13 外圈內(nèi)徑面熱酸洗磨削裂紋形貌
裝配質(zhì)量缺陷包括人為因素導(dǎo)致的磕碰傷或擠壓傷,裝配工藝不當(dāng)導(dǎo)致套圈局部受力較大,產(chǎn)生變形甚至斷裂,套圈保管或操作不規(guī)范會(huì)引起腐蝕及異物污染等。除裝配工藝不當(dāng)外,裝配質(zhì)量缺陷多為人為因素,而這是可以避免的。裝配過(guò)程中外圈局部掉塊如圖14所示。
圖14 裝配過(guò)程中外圈局部掉塊形貌
1.6 管理因素
管理因素主要指套圈各加工工序過(guò)程中由于人為因素引起的套圈機(jī)械傷(擠壓傷、磕碰傷、劃傷)以及腐蝕現(xiàn)象(酸蝕和銹蝕),其中以套圈腐蝕最為常見(jiàn),占套圈廢品比例約為10%。腐蝕現(xiàn)象在套圈滾道面最為常見(jiàn),其特征呈單一或者簇狀點(diǎn)狀缺陷(偶爾呈線(xiàn)狀),嚴(yán)重時(shí)呈凹坑狀;另外,軸承各個(gè)加工工序過(guò)程均有可能產(chǎn)生腐蝕現(xiàn)象。腐蝕現(xiàn)象雖受環(huán)境影響較大,但若操作規(guī)范完全可以避免。外圈滾道面點(diǎn)狀腐蝕缺陷形貌如圖15所示。
圖15 外圈溝道面點(diǎn)狀腐蝕缺陷形貌
2、預(yù)防措施
1)加強(qiáng)材料質(zhì)量檢驗(yàn)。根據(jù)統(tǒng)計(jì)分析,目前國(guó)內(nèi)軸承鋼質(zhì)量主要存在的問(wèn)題為表面缺陷,其次為非金屬夾雜物。尤其注意與設(shè)計(jì)及車(chē)加工結(jié)合,車(chē)除多余的材料缺陷;同時(shí),控制夾雜物尺寸,少數(shù)尺寸較大的夾雜物是應(yīng)力集中點(diǎn),易產(chǎn)生微裂紋,若分布在表面則造成套圈廢品或早期損壞;最后,碳化物不均勻性會(huì)影響套圈的熱處理質(zhì)量,造成力學(xué)性能不均,也會(huì)影響后續(xù)磨削加工(如熱處理變形磨削時(shí)易產(chǎn)生磨削燒傷)。通過(guò)加強(qiáng)材料檢驗(yàn),從源頭減少軸承套圈產(chǎn)生質(zhì)量問(wèn)題的概率。
2)優(yōu)化軸承套圈加工成形工藝。優(yōu)化熱處理工藝,減少套圈產(chǎn)生組織過(guò)熱或欠熱以及脫碳現(xiàn)象,盡量避免淬火應(yīng)力裂紋產(chǎn)生。優(yōu)化車(chē)削工藝,避免產(chǎn)生尖銳的車(chē)刀紋以及尖角毛刺等。同時(shí),根據(jù)套圈尺寸要求,盡可能多地車(chē)除材料原始缺陷。優(yōu)化磨削工藝,避免產(chǎn)生磨削燒傷和磨削裂紋。
軸研所公眾號(hào) 軸承雜志社公眾號(hào)
營(yíng)銷(xiāo)熱線(xiàn)
0379-64367521
0379-64880626
13693806700
0379-64880057
0379-64881181